- Home
- Blog
- Epe Length and Breadth Cutting Machine - Reliable Manufacturer, Supplier, Factory in China
Epe Length and Breadth Cutting Machine - Reliable Manufacturer, Supplier, Factory in China
By:admin
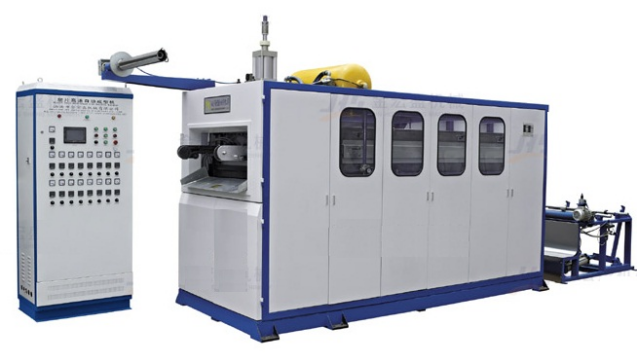
The state-of-the-art Epe Length and Breadth Cutting Machine is a revolutionary solution for efficient and accurate cutting of Epe foam material, offering incredible results in a fraction of the time. With its precision engineering and cutting-edge technology, this machine can effortlessly cut through tough Epe foam sheets, delivering flawless edges and a perfect finish every time.
The machine features a robust frame, sharp blades, and a user-friendly interface that allows for easy setting of the required cutting length and width. It also comes with a durable conveyor belt that ensures uninterrupted operations by swiftly transferring materials through the cutting blades.
Ms. Carlen Shu, a satisfied customer, expressed her admiration for the machine, highlighting its exceptional precision cutting and high-speed cutting ability. She emphasized that the user-friendly interface made it simple for even beginners to operate. Ms. Angela Her also praised the Epe Length and Breadth Cutting Machine for its efficiency, controlled movements, and compact size, making it an ideal option for businesses of all sizes.
Champion Machinery has been determined to expand its global strategy and explore international markets. The company has established a global agent network and has promoted and localized the Champion brand. They also pay visits to customers overseas for face-to-face communication to improve mutual understanding and customer service. Their footprints have been all over the world, including Asia, Europe, Oceania, North and South America, Africa, and the Middle East.
Champion Machinery's main products, including the Epe Length and Breadth Cutting Machine, are part of their "many" Product System, which consists of the 6 Series of Products. These series include Vacuum Forming, Recycling Plastic, Sheet Film Line, Blow/Injection Molding Machine, Hydraulic Cutting Machine, Air Compressor/Screw Compressor/Chiller/Hopper Dryer/Crusher/Mixer/Auto Loader, all in 1 intelligent integrated system solutions for Material Feeding, Air Supply, Water Supply, and Power Supply. The company efficiently meets customized demands based on their technical strength and supply chain advantages.
With their dedication to quality and innovation, Champion Machinery has become a reliable manufacturer in China, offering top-quality machines that guarantee efficient and cost-effective cutting operations. Whether for a manufacturing unit, workshop, or any workspace where daily cutting tasks are performed, investing in Champion's Epe Length and Breadth Cutting Machine ensures optimal accuracy and fast cutting speed without compromising on quality.
To learn more about how the cutting-edge Epe Length and Breadth Cutting Machine from Champion Machinery can help take your business to the next level, it is recommended to contact the company today. With a track record of providing exceptional products and expanding its global reach, Champion Machinery is a strategic partner for businesses looking to increase productivity and efficiency in their operations.
Company News & Blog
Advanced two color injection molding machine for efficient production
Two Color Injection Molding Machine Revolutionizes Production Processes In the highly competitive world of manufacturing, having the right tools and equipment can make a significant difference in productivity, efficiency, and ultimately, profitability. This is why the introduction of the two color injection molding machine by [company name removed] is generating a lot of buzz in the industry.The two color injection molding machine is a cutting-edge piece of equipment that allows manufacturers to produce complex, multi-colored parts with ease. This innovative machine is equipped with two injection units, which can inject two different materials or colors simultaneously, resulting in high-quality, two-color products with precision and speed.One of the key advantages of this machine is its ability to streamline the production process. Traditionally, manufacturing two-color parts required multiple molding processes and assembly steps, which not only increased production time but also added to the overall cost. With the two color injection molding machine, manufacturers can now produce two-color parts in a single cycle, saving time and reducing production costs.Additionally, the machine's advanced technology and precise control systems ensure consistent and uniform quality in the finished products, eliminating the need for secondary operations or adjustments. This not only enhances the overall product quality but also contributes to a more sustainable and environmentally-friendly production process.Moreover, the two color injection molding machine offers a wide range of applications across various industries, including automotive, consumer goods, electronics, and healthcare. It can produce a variety of products, such as automotive interior components, consumer electronics, medical devices, and household appliances, with intricate and aesthetic designs.[Company name removed] has built a strong reputation as a leading manufacturer of injection molding machines, with a focus on innovation, reliability, and customer satisfaction. The introduction of the two color injection molding machine is yet another example of the company's commitment to providing state-of-the-art solutions to its customers.The company's extensive experience and expertise in the field of injection molding machines have enabled them to develop this advanced technology to meet the evolving needs of the manufacturing industry. As a result, the two color injection molding machine has already garnered significant interest and demand from manufacturers looking to enhance their production capabilities.In addition to its innovative products, [company name removed] also offers comprehensive support and services to its customers. This includes technical assistance, training, and maintenance programs, ensuring that the two color injection molding machine operates at peak performance and efficiency, and that customers can maximize their return on investment.The company's commitment to quality, reliability, and customer satisfaction has earned them a loyal customer base and a strong presence in the global market. With the introduction of the two color injection molding machine, the company aims to further solidify its position as a leader in the industry and continue to drive innovation and progress in manufacturing processes.Overall, the two color injection molding machine by [company name removed] represents a significant advancement in production technology, offering manufacturers a more efficient, cost-effective, and versatile solution for producing high-quality, two-color parts. With its potential to transform production processes and drive business success, it is poised to make a lasting impact in the manufacturing industry.
Addressing Pollution: The Solution Lies in Biodegradable Plastics
Title: Biodegradable Plastic: The Ultimate Solution to Curb PollutionIntroductionEarth, our only home, is currently facing a serious threat to its life-supporting ability due to the alarming increase in pollution caused by human activities. Among the numerous factors contributing to this decline, the introduction of harmful substances into the environment and their subsequent impact on the ecosystem is a major concern. One such harmful substance is plastic, which has become a persistent problem worldwide. However, there is a potential solution that holds great promise in tackling this issue head-on: biodegradable plastic. In this blog post, we will explore the significance of biodegradable bags and the manufacturing machines that are revolutionizing the plastic industry.Understanding the Plastic Pollution CrisisPlastic has undoubtedly revolutionized various industries, offering convenience and versatility. However, the improper disposal and inadequate recycling of conventional plastic have resulted in a catastrophic environmental crisis. Traditional plastic takes hundreds of years to decompose, leading to the accumulation of plastic waste in landfills, water bodies, and even in the most remote corners of our planet. This not only harms wildlife and marine life but also poses a grave threat to human health.Biodegradable Plastic: A Sustainable AlternativeThe introduction of biodegradable plastic has emerged as a game-changer in the fight against plastic pollution. Unlike conventional plastic, biodegradable plastic has the unique ability to break down and decompose into natural elements over a relatively short period. This means that it does not leave lasting negative impacts on the environment. Biodegradable bags, made from this innovative material, are attracting global attention as a sustainable substitute for single-use plastic bags.Why Biodegradable Bags MatterBiodegradable bags offer a range of benefits when compared to traditional plastic bags. Firstly, they significantly reduce the burden on landfills and waste management systems, as they decompose effectively. Secondly, they do not contribute to the ever-growing plastic pollution crisis. Thirdly, the production process for biodegradable bags has a lower carbon footprint, making them more eco-friendly. Fourthly, these bags possess the same strength and durability as their conventional counterparts, ensuring that they can still serve their intended purpose without compromising on quality.The Role of Biodegradable Bag Manufacturing MachinesThe rapid shift towards biodegradable bags requires an efficient and cost-effective manufacturing process. This has led to the development of advanced biodegradable bag manufacturing machines. These machines utilize cutting-edge technology to produce high-quality biodegradable bags in large quantities. With precise control over parameters such as size, thickness, and material composition, manufacturers can cater to diverse industrial and consumer needs.Keywords: Biodegradable Bags Manufacturing MachineTo ensure optimal visibility in search engine results, it is crucial to incorporate relevant keywords into the content. The focus keyword for this article, "Biodegradable Bags Manufacturing Machine," helps target readers actively seeking information on this specific topic. By naturally including this keyword throughout the blog post, we can enhance its relevance and visibility on search engines, thus boosting its search engine optimization (SEO) potential.ConclusionThe plastic pollution crisis is a global concern that demands immediate action. Biodegradable plastic, particularly in the form of biodegradable bags, offers a viable solution to curbing pollution and preserving our planet for future generations. As awareness grows and technology advances, incorporating biodegradable bags manufacturing machines into industry practices will help accelerate the transition towards a sustainable future. By embracing this eco-friendly alternative, we can pave the way for a cleaner, greener, and healthier planet Earth.
How to Set Cues in a Lighting Control Console Series 200 Monitor
Strand, a leading lighting control console manufacturer, has released its latest product line - the Strand 200 series. This series offers a new level of flexibility and control for lighting designers and technicians, making it an essential tool for any production or event.The Strand 200 series offers a range of features that will enhance the experience of any lighting designer. First, the lighting control console is equipped with a 24-48 channel console, making it ideal for a wide range of lighting setups. It offers a range of programmable memory scenes, allowing for easy recall of previously saved cues. Additionally, the console provides real-time feedback of lighting levels and timings, allowing for quick adjustments and modifications to the lighting design.One of the key features of the Strand 200 series is its ability to set cues. This is an essential task when creating a lighting design, allowing the technician to select the specific lighting levels and timings needed for each specific moment in the production. Within the Strand 200 series, setting cues is a simple process that can be done quickly and efficiently, thanks to the console's intuitive design.To set a cue in the Strand 200 series, technicians simply need to select the desired channel and adjust the lighting level as needed. Once the desired level is set, the technician can choose to save the cue as a new scene or to modify an existing scene to include the new cue. This process can be repeated for each desired cue, allowing for a fully customized lighting design.Another key feature of the Strand 200 series is its ability to be used in conjunction with the MX Board series. This can provide additional flexibility and control, allowing for more complex lighting designs to be created. The console's ability to control up to 48 channels makes it ideal for use in larger productions, where a more comprehensive lighting setup is needed.Overall, the Strand 200 series is an impressive addition to the lighting control console landscape. With its range of features, ease of use, and compatibility with other hardware, it is sure to be a valuable tool for any lighting technician or designer. Whether used in small productions or large events, the Strand 200 series is a top choice for those in need of high-quality lighting control.
Understanding the Importance of Injection Speed in Injection Molding
Injection Speed In Injection MoldingInjection molding is a widely used manufacturing process for producing parts by injecting material into a mold. One of the crucial factors that determine the quality and efficiency of the process is the injection speed. Injection speed refers to the speed at which the material is injected into the mold. It plays a vital role in the overall production process, affecting the final product's quality, surface finish, and overall cycle time.Leading in the industry is {} (Company), a global leader in industrial manufacturing solutions. The company has a proven track record of providing high-quality injection molding machines and solutions to various industries worldwide.One of the key features of {}'s injection molding machines is their ability to control and adjust injection speed. This allows for a precise and efficient molding process, resulting in high-quality and consistent parts production.With the injection speed being a critical factor in the injection molding process, {} has developed state-of-the-art technology to ensure optimal performance. The company's injection molding machines are equipped with advanced control systems that allow operators to precisely adjust and monitor the injection speed, providing flexibility and control over the production process.Furthermore, {}'s injection molding machines are designed to achieve high injection speeds without compromising on the quality of the final product. This is achieved through innovative design and engineering, as well as the use of high-quality materials and components.The ability to adjust injection speed according to the specific requirements of each part and material is crucial in achieving the desired results. {}'s injection molding machines offer a wide range of injection speed options, allowing for versatility in production and ensuring that each part is manufactured with precision and accuracy.In addition to providing high-quality injection molding machines, {} also offers comprehensive support and solutions to its customers. The company's team of experts is dedicated to helping businesses optimize their production processes, providing guidance on injection speed optimization and other factors that can impact the overall efficiency and quality of production.{}'s commitment to innovation and excellence has made it a trusted partner for businesses looking to enhance their injection molding capabilities. With its advanced injection molding machines and expertise in injection speed control, {} continues to set the standard for quality and performance in the industry.In conclusion, injection speed is a critical factor in the injection molding process, and {} has proven itself as a leader in providing high-quality injection molding machines with advanced injection speed control capabilities. With its commitment to innovation and excellence, {} is a valuable partner for businesses looking to achieve optimal results in their injection molding operations.
Stretch Film Machine Manufacturer, Supplier, and Factory in China
Champion Machinery Expands Global Reach with High-Quality Stretch Film MachineChampion Machinery, a leading manufacturer and supplier in China, is proud to announce the launch of their advanced stretch film machine, designed to meet the growing demand for high-quality packaging and transportation solutions in international markets.With a strong focus on exploring international markets, Champion Machinery has established a global agent network and promoted the localization of their brand. This strategic initiative has enabled the company to expand its footprint across Asia, Europe, Oceania, North and South America, Africa, and the Middle East. By paying visits to customers overseas for face-to-face communication, Champion Machinery has been able to improve mutual understanding and provide enhanced service to customers around the world.The newly launched Colines Stretch Film Machine is a state-of-the-art wrapping solution that is ideal for use in industrial settings. It is designed to produce high-quality stretch films at impressive speeds, making it perfect for companies that require fast and efficient production. The machine is highly versatile and can produce a range of films that meet different requirements, including standard stretch film, pre-stretch film, and super-stretch film.One of the key features of the Colines Stretch Film Machine is its flexibility. It can be used to produce films of varying widths and thicknesses, and the speed of production can be easily adjusted to meet specific needs. This level of customization ensures that businesses can efficiently meet their packaging and transportation requirements.Additionally, the machine is equipped with advanced safety features, ensuring that operators can work safely and efficiently in any environment. The intuitive interface allows operators to easily control and adjust the machine settings, making it simple to use for even the most inexperienced machine operators.Customer reviews of the Colines Stretch Film Machine have been overwhelmingly positive. Ms. Carlen Shu, a satisfied customer, remarked, "The Colines Stretch Film Machine is a fantastic addition to any industrial packaging facility. This top-of-the-line machine is designed to produce high-quality stretch film quickly and efficiently, making it an excellent choice for businesses looking to increase their productivity and output."Ms. Angela Her, another customer, described the machine as "an excellent industrial-grade equipment for producing high-quality stretch film." She emphasized the machine's efficiency, ease of use, and top-notch build quality, making it an excellent investment for businesses looking to improve their stretch film production capabilities.Champion Machinery's commitment to providing high-performance and durable equipment is evident in the advanced technology incorporated into the Colines Stretch Film Machine. The machine is an ideal investment for businesses looking to improve their packaging and transportation efficiency, reduce waste, and save costs.In addition to the Colines Stretch Film Machine, Champion Machinery offers a range of customizable options to meet the diverse requirements of different businesses. The company's product system includes six series of products, encompassing vacuum forming, recycling plastic, sheet film line, blow/injection molding machines, EPE foam machines, hydraulic cutting machines, and integrated system solutions for material feeding, air supply, water supply, and power supply.By leveraging their technical strength and supply chain advantages, Champion Machinery efficiently meets the customized demand for intelligent integrated system solutions. This dedication to excellence sets the company apart as a reliable and innovative provider of industrial packaging equipment.As Champion Machinery continues to expand its global reach, customers worldwide can look forward to accessing high-quality machinery and exceptional service. With a focus on delivering reliable and efficient solutions, the company is well-positioned to meet the evolving needs of businesses in diverse industries.In conclusion, the launch of the Colines Stretch Film Machine underscores Champion Machinery's commitment to delivering cutting-edge solutions for industrial packaging. With a growing presence in international markets, the company is poised to make a significant impact on the global packaging and transportation industry. Businesses searching for top-quality stretch film machines can turn to Champion Machinery for advanced technology, reliable performance, and superior customer service.
High-quality Sheet Cutting Machine for PP Materials
Pp Sheet Cutting Machine Revolutionizing the Manufacturing IndustryWith the continuous development of science and technology, the manufacturing industry is constantly seeking new equipment and machinery to improve efficiency and productivity. One such innovation that has made a significant impact is the Pp Sheet Cutting Machine, which has revolutionized the way companies process and cut polypropylene sheets.The Pp Sheet Cutting Machine, developed by a leading machinery manufacturer, is designed to meet the growing demand for precise and efficient cutting of polypropylene sheets. This machine is equipped with advanced technology and features that allow for high-speed cutting, precise measurements, and minimal material waste. Its automated cutting process ensures consistent and accurate cuts, making it ideal for a wide range of industries, including packaging, automotive, construction, and more.The company behind the Pp Sheet Cutting Machine has established itself as a trusted leader in the manufacturing industry. With a strong emphasis on research and development, the company has continuously introduced innovative solutions to meet the evolving needs of its customers. Its commitment to quality and excellence has earned it a reputation for delivering dependable and high-performance machinery that helps businesses streamline their production processes and improve overall efficiency.The Pp Sheet Cutting Machine is a testament to the company's dedication to innovation and customer satisfaction. By combining cutting-edge technology with user-friendly design, the machine has set a new standard for precision and speed in the cutting of polypropylene sheets. Its versatility and adaptability make it a valuable asset for manufacturers looking to enhance their operations and stay ahead of the competition.One of the key features of the Pp Sheet Cutting Machine is its ability to handle a wide range of sheet sizes and thicknesses. Whether working with thin films or thick sheets, the machine can accommodate various materials with ease, making it a versatile solution for diverse manufacturing needs. Additionally, the machine's intuitive controls and programmable settings make it easy to set up and operate, minimizing downtime and maximizing productivity.The Pp Sheet Cutting Machine also prioritizes safety and efficiency, incorporating safeguards and automation to reduce the risk of accidents and errors. This not only protects workers but also ensures consistent and reliable output, contributing to a more seamless production process. As a result, businesses can enhance their operational efficiency while maintaining a safe and secure working environment.Furthermore, the Pp Sheet Cutting Machine aligns with the growing emphasis on sustainability and resource efficiency in the manufacturing industry. By minimizing material waste and optimizing cutting processes, the machine helps companies make more environmentally friendly choices without compromising on quality and performance. This underscores the company's commitment to advancing sustainable solutions and supporting eco-conscious manufacturing practices.The introduction of the Pp Sheet Cutting Machine represents a significant milestone in the manufacturing industry, offering a cutting-edge solution to meet the evolving demands of modern production processes. By combining precision, speed, and versatility, the machine empowers businesses to elevate their operations and achieve new levels of efficiency and quality.In conclusion, the Pp Sheet Cutting Machine has emerged as a game-changer for the manufacturing industry, embodying the company's dedication to innovation, quality, and customer satisfaction. As businesses continue to seek ways to optimize their production processes, this advanced cutting machine stands out as a reliable and effective solution. With its superior performance, user-friendly design, and focus on safety and sustainability, the Pp Sheet Cutting Machine is poised to shape the future of manufacturing for years to come.
Unlocking the Potential of Precision Plastic Machining for Prominent Industries
[Company Introduction]:Precision Plastic Machining (PPM) is a leading provider of high-quality plastic machining solutions. With a strong focus on precision, PPM utilizes advanced technology and state-of-the-art equipment to manufacture plastic components with exceptional accuracy and reliability. With years of industry expertise, PPM has built a reputation for delivering outstanding results and exceeding customer expectations.[News Content]:Title: Innovative Plastic Machining Solutions Revolutionize the IndustrySubtitle: Precision Plastic Machining (PPM) introduces cutting-edge manufacturing techniques for better efficiency and quality.[City, Date] - Precision Plastic Machining (PPM), a prominent player in the plastic machining industry, is making waves with its innovative manufacturing techniques that bring unparalleled efficiency and quality to the market. By combining advanced technology with a team of highly skilled professionals, PPM is redefining the standards of precision plastic machining.With a commitment to providing the best solutions for its clients, PPM has invested heavily in state-of-the-art equipment and software. This allows them to deliver precision-machined plastic components that meet the most stringent requirements of various industries, including aerospace, automotive, electronics, and medical devices.One of the key factors that sets PPM apart from its competitors is its focus on quality control. By employing rigorous inspection processes throughout the manufacturing cycle, PPM ensures that every component leaving its facility adheres to the highest industry standards. This dedication to quality has earned PPM numerous accolades and the trust of its diverse clientele.One of the breakthrough technologies employed by PPM is the use of computer numerical control (CNC) machining. This technique enables PPM to produce complex plastic parts with exceptional accuracy and precision. By harnessing the power of CNC machining, PPM eliminates the limitations of traditional machining methods, resulting in higher productivity and lower production costs.In addition to CNC machining, PPM utilizes 3D printing technology to create prototypes and low-volume production runs. This cost-effective method allows their clients to test and refine designs quickly, reducing time-to-market and increasing overall efficiency. By embracing these cutting-edge manufacturing techniques, PPM continues to push the boundaries of what is possible in the plastic machining industry.PPM's dedication to sustainability is also worth mentioning. They actively pursue environmentally friendly processes and material recycling to minimize their carbon footprint. By focusing on sustainable practices, PPM ensures that their manufacturing processes align with global efforts to reduce waste and conserve resources.Furthermore, PPM emphasizes collaboration and partnership with its clients. The company's team of highly skilled engineers and technicians work closely with customers to understand their unique requirements and provide tailored solutions. This personalized approach has resulted in long-lasting relationships with clients who appreciate the commitment PPM brings to every project."We are proud to be at the forefront of the industry, offering innovative plastic machining solutions that address the evolving needs of our customers," said [Name], [Position] at PPM. "By combining advanced technology, exceptional talent, and a passion for quality, we are confident in our ability to drive innovation and create value for our clients."With its relentless pursuit of excellence, Precision Plastic Machining (PPM) continues to revolutionize the plastic machining industry. Their commitment to precision, quality, sustainability, and customer satisfaction sets them apart and positions them as an industry leader. As PPM continues to push boundaries and explore new techniques, they are poised to shape the future of plastic machining.
High-Density Polyethylene: A Guide to CNC Machining and Applications
CNC HDPE, a leading manufacturer of high-density polyethylene (HDPE) products, has recently expanded its product line to include a new range of cutting-edge HDPE materials. The company has invested heavily in research and development to create these innovative materials, which offer superior performance and durability compared to traditional HDPE products. This latest development underscores CNC HDPE's commitment to providing its customers with the highest quality materials for their specific needs.HDPE is a versatile material that is widely used in a variety of industries, including construction, packaging, and agriculture. It is known for its strength, chemical resistance, and overall durability. However, CNC HDPE has taken these characteristics to the next level by introducing a new line of HDPE materials that are even more robust and long-lasting.One of the key features of CNC HDPE's new materials is their improved impact resistance. This makes them ideal for applications where the material will be subjected to high levels of stress or wear and tear. Additionally, the new materials offer enhanced resistance to harsh chemicals, making them suitable for use in environments where traditional HDPE materials may not be suitable.Moreover, CNC HDPE's new HDPE materials are designed to be easily machinable, making them a perfect choice for customers who require precision components. The materials can be easily shaped and formed to meet the specific requirements of a wide range of applications, from industrial machinery components to intricate consumer products.In addition to their superior performance characteristics, CNC HDPE's new materials are also more environmentally friendly than traditional HDPE products. The company has invested in developing materials that are fully recyclable, reducing the environmental impact of the manufacturing process and providing a sustainable solution for its customers.CNC HDPE's dedication to innovation and quality is reflected in its state-of-the-art manufacturing facilities. The company's production processes are designed to ensure the highest standards of quality and consistency in every product it manufactures. With a focus on precision and efficiency, CNC HDPE is able to deliver high-quality materials to its customers in a timely manner.The company's commitment to customer satisfaction is also evident in its dedication to providing exceptional service and support. CNC HDPE's team of experts is available to assist customers with selecting the right materials for their specific needs and to provide technical guidance throughout the manufacturing process. This level of support ensures that customers can confidently choose CNC HDPE as their trusted partner for all their HDPE material needs.CNC HDPE's new line of cutting-edge HDPE materials represents the company's ongoing dedication to pushing the boundaries of what is possible with this versatile material. By investing in research and development, CNC HDPE continues to set the standard for quality and innovation in the HDPE industry. This latest development is a testament to the company's commitment to meeting the evolving needs of its customers and providing them with the best possible solutions for their specific applications.As CNC HDPE continues to expand its product line and enhance its manufacturing capabilities, customers can expect even more groundbreaking developments in the future. With a focus on quality, performance, and sustainability, CNC HDPE is poised to remain a leader in the HDPE industry for years to come.
Small Scale Plastic Bottle Making Machine - Manufacturer, Supplier, Factory in China
Champion Machinery has recently made significant strides in their global strategy, with a focus on exploring international markets and establishing a strong global agent network. The company has been actively promoting and localizing the Champion brand, with a strong presence in Asia, Europe, Oceania, North and South America, Africa, and the Middle East.One of Champion Machinery's main products is the Small Scale Plastic Bottle Making Machine, which has gained recognition for its high-quality and cost-effective solutions. The company has been dedicated to providing efficient and reliable manufacturing equipment to meet the demands of small businesses and startups looking to produce their own plastic bottles.The Small Scale Plastic Bottle Making Machine offered by Champion Machinery is designed with compactness and efficiency in mind. It can produce up to 500 bottles per hour with precision and consistency, making it an ideal solution for businesses looking to streamline their production process. The machine is user-friendly, requiring minimal maintenance and offering easy operation, which is crucial for small businesses or start-ups.Additionally, the Small Scale Plastic Bottle Making Machine is constructed from high-quality materials, ensuring durability and longevity. It is also environmentally-friendly, using minimal resources and energy to operate, and it offers a cost-effective solution for businesses looking to produce their own plastic bottles.Customer reviews have highlighted the machine's efficiency, durability, and affordability. Users have praised its ease of use, high-quality production, and low maintenance costs, making it an excellent investment for businesses that require small quantities of plastic bottles.Champion Machinery's commitment to providing high-quality manufacturing equipment is evident in their dedication to customer service and their continuous efforts to improve their products and services. The company's global presence and strong agent network enable them to provide face-to-face communication with customers overseas, leading to improved mutual understanding and enhanced service.In addition to the Small Scale Plastic Bottle Making Machine, Champion Machinery offers a wide range of products including Vacuum Forming, Recycling Plastic, Sheet Film Line, Blow/Injection Molding Machine, EPE Foam Machine, Hydraulic Cutting Machine, and various integrated system solutions for Material Feeding, Air Supply, Water Supply, and Power Supply. The company's technical strength and supply chain advantages allow them to efficiently meet customized demands.With a strong emphasis on quality, efficiency, and customer satisfaction, Champion Machinery continues to be a reliable partner for businesses looking to enhance their production capabilities. The company's dedication to innovation and their comprehensive range of manufacturing equipment make them a go-to source for small scale plastic bottle making machines and other related products.In conclusion, Champion Machinery's Small Scale Plastic Bottle Making Machine stands out as a top-quality and efficient solution for businesses looking to produce their own plastic bottles. With its user-friendly design, durability, and cost-effectiveness, the machine offers a competitive advantage for small businesses and startups in the plastic bottle production industry. As the company continues to expand its global presence and enhance its product offerings, Champion Machinery remains a trusted manufacturer and supplier for businesses worldwide.
Co-Extrusion Plastic Sheet Extruder: Discover the Latest Advancements
Title: New Co-Extrusion Plastic Sheet Extruder Revolutionizes Manufacturing IndustryIntroduction:In an ever-evolving world of technology and innovation, the manufacturing industry has witnessed yet another groundbreaking development. This development comes in the form of the Pp/Ps Co-Extrusion Plastic Sheet Extruder, a revolutionary machine that promises to transform the way plastic sheets are produced. With its advanced capabilities and efficiency, this innovative equipment is poised to revolutionize the manufacturing sector.I. Overview of Co-Extrusion Technology:Co-extrusion technology involves the simultaneous extrusion of multiple materials through a single die, resulting in a plastic sheet with improved properties and characteristics. This method allows different layers to be combined, offering a wide range of possibilities in terms of material compatibility and product versatility. The Pp/Ps Co-Extrusion Plastic Sheet Extruder harnesses the power of this technology to offer manufacturers unprecedented control and flexibility in their plastic sheet production processes.II. Features and Benefits:The state-of-the-art Pp/Ps Co-Extrusion Plastic Sheet Extruder boasts several remarkable features that set it apart from traditional plastic extruders:1. Enhanced Efficiency: The machine's cutting-edge design and advanced control systems enable a significant increase in production rates. The co-extrusion process ensures high material utilization and reduces waste, leading to improved overall efficiency.2. Versatility: With the ability to combine different types of plastic materials, the extruder caters to a wide range of applications. Manufacturers can produce sheets with varying thicknesses, colors, textures, and even incorporate functional additives to enhance specific properties.3. Material Compatibility: The Pp/Ps Co-Extrusion Plastic Sheet Extruder offers manufacturers the freedom to utilize a variety of materials with varying melt temperatures. This flexibility eliminates the need for material compromises, ultimately resulting in superior product performance.4. Cost Optimization: By utilizing the co-extrusion process, manufacturers can economize material usage, reducing costs associated with raw materials. The machine's efficient production capabilities also contribute to cost savings, allowing businesses to remain competitive in today's challenging market.III. Applications and Industry Implications:The introduction of the Pp/Ps Co-Extrusion Plastic Sheet Extruder has profound implications for numerous industries:1. Packaging: This extruder can produce plastic sheets with superior strength and resilience, making them ideal for packaging applications. The ability to co-extrude different materials can also result in multi-layered sheets that offer enhanced barrier properties.2. Construction: The extruder's versatility enables the production of thermally efficient and durable plastic sheets suitable for a wide range of construction applications. These sheets can serve as insulation barriers, weather-resistant claddings, or even as decorative elements in architectural projects.3. Automotive: The automotive industry can benefit from the exceptional material properties and design capabilities the extruder offers. Manufacturers can create lightweight plastic sheets with high strength, impact resistance, and aesthetics, contributing to overall vehicle performance and design improvements.IV. Company's Commitment to Sustainable Manufacturing:The company behind the Pp/Ps Co-Extrusion Plastic Sheet Extruder understands the importance of sustainability in today's business landscape. As such, the machine incorporates various eco-friendly features:1. Energy Efficiency: The extruder is designed to minimize energy consumption, contributing to reduced carbon emissions and ecological impact.2. Recyclability: The utilization of recyclable thermoplastic materials within the co-extrusion process supports the circular economy principles, reducing plastic waste and promoting sustainability.Conclusion:The introduction of the Pp/Ps Co-Extrusion Plastic Sheet Extruder marks a significant milestone in the manufacturing industry. By harnessing the power of co-extrusion technology, this innovative machine empowers manufacturers with unprecedented control, versatility, and efficiency in their plastic sheet production processes. With its countless applications across various industries, the extruder promises to shape the future of plastic sheet manufacturing while championing sustainable practices.
Advanced two color injection molding machine for efficient production
Two Color Injection Molding Machine Revolutionizes Production Processes In the highly competitive world of manufacturing, having the right tools and equipment can make a significant difference in productivity, efficiency, and ultimately, profitability. This is why the introduction of the two color injection molding machine by [company name removed] is generating a lot of buzz in the industry.The two color injection molding machine is a cutting-edge piece of equipment that allows manufacturers to produce complex, multi-colored parts with ease. This innovative machine is equipped with two injection units, which can inject two different materials or colors simultaneously, resulting in high-quality, two-color products with precision and speed.One of the key advantages of this machine is its ability to streamline the production process. Traditionally, manufacturing two-color parts required multiple molding processes and assembly steps, which not only increased production time but also added to the overall cost. With the two color injection molding machine, manufacturers can now produce two-color parts in a single cycle, saving time and reducing production costs.Additionally, the machine's advanced technology and precise control systems ensure consistent and uniform quality in the finished products, eliminating the need for secondary operations or adjustments. This not only enhances the overall product quality but also contributes to a more sustainable and environmentally-friendly production process.Moreover, the two color injection molding machine offers a wide range of applications across various industries, including automotive, consumer goods, electronics, and healthcare. It can produce a variety of products, such as automotive interior components, consumer electronics, medical devices, and household appliances, with intricate and aesthetic designs.[Company name removed] has built a strong reputation as a leading manufacturer of injection molding machines, with a focus on innovation, reliability, and customer satisfaction. The introduction of the two color injection molding machine is yet another example of the company's commitment to providing state-of-the-art solutions to its customers.The company's extensive experience and expertise in the field of injection molding machines have enabled them to develop this advanced technology to meet the evolving needs of the manufacturing industry. As a result, the two color injection molding machine has already garnered significant interest and demand from manufacturers looking to enhance their production capabilities.In addition to its innovative products, [company name removed] also offers comprehensive support and services to its customers. This includes technical assistance, training, and maintenance programs, ensuring that the two color injection molding machine operates at peak performance and efficiency, and that customers can maximize their return on investment.The company's commitment to quality, reliability, and customer satisfaction has earned them a loyal customer base and a strong presence in the global market. With the introduction of the two color injection molding machine, the company aims to further solidify its position as a leader in the industry and continue to drive innovation and progress in manufacturing processes.Overall, the two color injection molding machine by [company name removed] represents a significant advancement in production technology, offering manufacturers a more efficient, cost-effective, and versatile solution for producing high-quality, two-color parts. With its potential to transform production processes and drive business success, it is poised to make a lasting impact in the manufacturing industry.
Addressing Pollution: The Solution Lies in Biodegradable Plastics
Title: Biodegradable Plastic: The Ultimate Solution to Curb PollutionIntroductionEarth, our only home, is currently facing a serious threat to its life-supporting ability due to the alarming increase in pollution caused by human activities. Among the numerous factors contributing to this decline, the introduction of harmful substances into the environment and their subsequent impact on the ecosystem is a major concern. One such harmful substance is plastic, which has become a persistent problem worldwide. However, there is a potential solution that holds great promise in tackling this issue head-on: biodegradable plastic. In this blog post, we will explore the significance of biodegradable bags and the manufacturing machines that are revolutionizing the plastic industry.Understanding the Plastic Pollution CrisisPlastic has undoubtedly revolutionized various industries, offering convenience and versatility. However, the improper disposal and inadequate recycling of conventional plastic have resulted in a catastrophic environmental crisis. Traditional plastic takes hundreds of years to decompose, leading to the accumulation of plastic waste in landfills, water bodies, and even in the most remote corners of our planet. This not only harms wildlife and marine life but also poses a grave threat to human health.Biodegradable Plastic: A Sustainable AlternativeThe introduction of biodegradable plastic has emerged as a game-changer in the fight against plastic pollution. Unlike conventional plastic, biodegradable plastic has the unique ability to break down and decompose into natural elements over a relatively short period. This means that it does not leave lasting negative impacts on the environment. Biodegradable bags, made from this innovative material, are attracting global attention as a sustainable substitute for single-use plastic bags.Why Biodegradable Bags MatterBiodegradable bags offer a range of benefits when compared to traditional plastic bags. Firstly, they significantly reduce the burden on landfills and waste management systems, as they decompose effectively. Secondly, they do not contribute to the ever-growing plastic pollution crisis. Thirdly, the production process for biodegradable bags has a lower carbon footprint, making them more eco-friendly. Fourthly, these bags possess the same strength and durability as their conventional counterparts, ensuring that they can still serve their intended purpose without compromising on quality.The Role of Biodegradable Bag Manufacturing MachinesThe rapid shift towards biodegradable bags requires an efficient and cost-effective manufacturing process. This has led to the development of advanced biodegradable bag manufacturing machines. These machines utilize cutting-edge technology to produce high-quality biodegradable bags in large quantities. With precise control over parameters such as size, thickness, and material composition, manufacturers can cater to diverse industrial and consumer needs.Keywords: Biodegradable Bags Manufacturing MachineTo ensure optimal visibility in search engine results, it is crucial to incorporate relevant keywords into the content. The focus keyword for this article, "Biodegradable Bags Manufacturing Machine," helps target readers actively seeking information on this specific topic. By naturally including this keyword throughout the blog post, we can enhance its relevance and visibility on search engines, thus boosting its search engine optimization (SEO) potential.ConclusionThe plastic pollution crisis is a global concern that demands immediate action. Biodegradable plastic, particularly in the form of biodegradable bags, offers a viable solution to curbing pollution and preserving our planet for future generations. As awareness grows and technology advances, incorporating biodegradable bags manufacturing machines into industry practices will help accelerate the transition towards a sustainable future. By embracing this eco-friendly alternative, we can pave the way for a cleaner, greener, and healthier planet Earth.
How to Set Cues in a Lighting Control Console Series 200 Monitor
Strand, a leading lighting control console manufacturer, has released its latest product line - the Strand 200 series. This series offers a new level of flexibility and control for lighting designers and technicians, making it an essential tool for any production or event.The Strand 200 series offers a range of features that will enhance the experience of any lighting designer. First, the lighting control console is equipped with a 24-48 channel console, making it ideal for a wide range of lighting setups. It offers a range of programmable memory scenes, allowing for easy recall of previously saved cues. Additionally, the console provides real-time feedback of lighting levels and timings, allowing for quick adjustments and modifications to the lighting design.One of the key features of the Strand 200 series is its ability to set cues. This is an essential task when creating a lighting design, allowing the technician to select the specific lighting levels and timings needed for each specific moment in the production. Within the Strand 200 series, setting cues is a simple process that can be done quickly and efficiently, thanks to the console's intuitive design.To set a cue in the Strand 200 series, technicians simply need to select the desired channel and adjust the lighting level as needed. Once the desired level is set, the technician can choose to save the cue as a new scene or to modify an existing scene to include the new cue. This process can be repeated for each desired cue, allowing for a fully customized lighting design.Another key feature of the Strand 200 series is its ability to be used in conjunction with the MX Board series. This can provide additional flexibility and control, allowing for more complex lighting designs to be created. The console's ability to control up to 48 channels makes it ideal for use in larger productions, where a more comprehensive lighting setup is needed.Overall, the Strand 200 series is an impressive addition to the lighting control console landscape. With its range of features, ease of use, and compatibility with other hardware, it is sure to be a valuable tool for any lighting technician or designer. Whether used in small productions or large events, the Strand 200 series is a top choice for those in need of high-quality lighting control.
Understanding the Importance of Injection Speed in Injection Molding
Injection Speed In Injection MoldingInjection molding is a widely used manufacturing process for producing parts by injecting material into a mold. One of the crucial factors that determine the quality and efficiency of the process is the injection speed. Injection speed refers to the speed at which the material is injected into the mold. It plays a vital role in the overall production process, affecting the final product's quality, surface finish, and overall cycle time.Leading in the industry is {} (Company), a global leader in industrial manufacturing solutions. The company has a proven track record of providing high-quality injection molding machines and solutions to various industries worldwide.One of the key features of {}'s injection molding machines is their ability to control and adjust injection speed. This allows for a precise and efficient molding process, resulting in high-quality and consistent parts production.With the injection speed being a critical factor in the injection molding process, {} has developed state-of-the-art technology to ensure optimal performance. The company's injection molding machines are equipped with advanced control systems that allow operators to precisely adjust and monitor the injection speed, providing flexibility and control over the production process.Furthermore, {}'s injection molding machines are designed to achieve high injection speeds without compromising on the quality of the final product. This is achieved through innovative design and engineering, as well as the use of high-quality materials and components.The ability to adjust injection speed according to the specific requirements of each part and material is crucial in achieving the desired results. {}'s injection molding machines offer a wide range of injection speed options, allowing for versatility in production and ensuring that each part is manufactured with precision and accuracy.In addition to providing high-quality injection molding machines, {} also offers comprehensive support and solutions to its customers. The company's team of experts is dedicated to helping businesses optimize their production processes, providing guidance on injection speed optimization and other factors that can impact the overall efficiency and quality of production.{}'s commitment to innovation and excellence has made it a trusted partner for businesses looking to enhance their injection molding capabilities. With its advanced injection molding machines and expertise in injection speed control, {} continues to set the standard for quality and performance in the industry.In conclusion, injection speed is a critical factor in the injection molding process, and {} has proven itself as a leader in providing high-quality injection molding machines with advanced injection speed control capabilities. With its commitment to innovation and excellence, {} is a valuable partner for businesses looking to achieve optimal results in their injection molding operations.